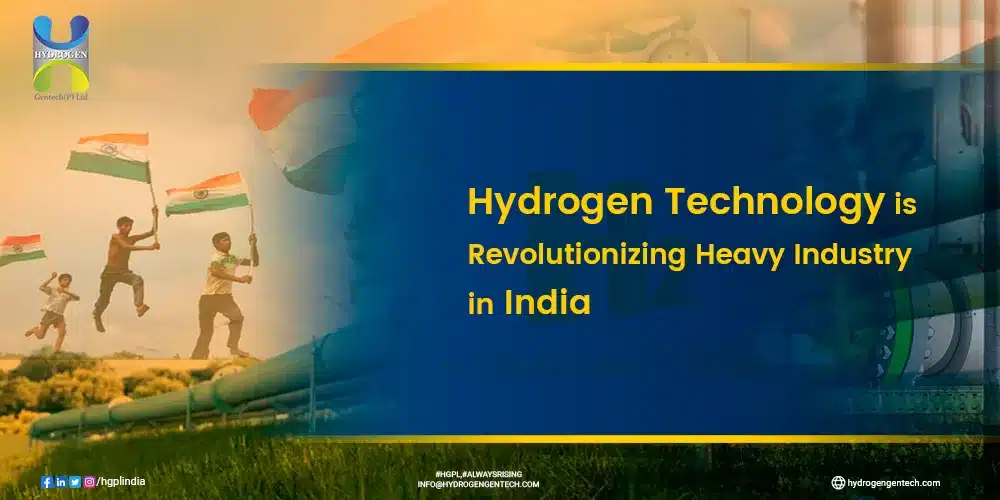
The rapid adoption of hydrogen technology is set to transform India’s heavy industry landscape. As a country with ambitious carbon reduction goals, India is focusing on alternative energy sources that can decarbonize sectors known for their high greenhouse gas emissions. Among these sectors, steel, cement, and chemical production are prime candidates for revolutionary changes through the application of hydrogen technology. The move towards hydrogen-powered technologies offers India a sustainable, cleaner, and more efficient energy solution, enabling industries to reduce their carbon footprint while remaining competitive on the global stage.
The Heavy Industry Challenge: Decarbonizing Steel, Cement, and Chemicals
Heavy industries, particularly steel, cement, and chemical production, are responsible for a significant share of India’s total carbon emissions. These industries rely heavily on fossil fuels, such as coal and natural gas, to power their energy-intensive processes. Despite their critical role in supporting infrastructure and economic development, these sectors face mounting pressure to reduce their environmental impact in light of India’s pledge to achieve net-zero emissions by 2070.
- Steel Industry:
The steel industry is one of the most carbon-intensive industries, contributing approximately 7-9% of global CO2 emissions. In India, which is the second-largest steel producer in the world, traditional blast furnaces use coal as a primary energy source for iron ore reduction. This process releases a considerable amount of CO2 into the atmosphere. - Cement Industry:
Cement production is responsible for about 8% of global CO2 emissions. The manufacturing process, particularly the heating of limestone to produce clinker, involves substantial energy consumption and direct emissions of carbon dioxide from the raw materials. - Chemical Industry:
The chemical industry is another major emitter, with large-scale production of chemicals such as ammonia, fertilizers, and plastics relying on fossil fuels. Processes like the Haber-Bosch method for ammonia production are highly energy-intensive and release significant amounts of greenhouse gases.
Hydrogen: The Game Changer for Heavy Industry
Hydrogen technology offers a pathway to drastically reduce or eliminate emissions from these industries. As a versatile and clean fuel, hydrogen can be used to replace fossil fuels in various industrial processes, offering an opportunity for deep decarbonization.
- Hydrogen in Steel Production:
One of the most promising applications of hydrogen in heavy industry is in steel production. Hydrogen can be used as a reducing agent in place of coke (derived from coal) in the direct reduction of iron ore. This process, known as Direct Reduced Iron (DRI) using hydrogen, emits water vapor instead of CO2, making it a clean alternative. India’s steel manufacturers are beginning to explore this technology, with pilot projects already underway to assess the feasibility of using hydrogen in large-scale production.For instance, Tata Steel, one of India’s largest steel producers, has initiated hydrogen-based steelmaking projects. By using green hydrogen generated from renewable energy, they aim to significantly cut down their carbon emissions, aligning with India’s green steel mission. - Hydrogen in Cement Production:
Cement production involves high-temperature kilns that require vast amounts of energy, typically derived from coal. Hydrogen can be used to fuel these kilns, replacing traditional fossil fuels. Although the cement industry is still in the early stages of hydrogen adoption, research and development efforts are advancing rapidly to integrate hydrogen into the cement-making process.By leveraging hydrogen for heat generation, the cement industry can not only reduce its carbon emissions but also improve the energy efficiency of the production process. Additionally, the use of green hydrogen (produced via electrolysis using renewable energy) would provide a completely sustainable solution for energy-intensive cement production. - Hydrogen in the Chemical Industry:
The chemical industry presents numerous opportunities for hydrogen utilization, particularly in processes such as ammonia production and petrochemical refining. In ammonia production, for example, hydrogen can replace the conventional hydrogen derived from natural gas reforming. Green hydrogen produced via electrolysis can power the Haber-Bosch process, resulting in the production of ammonia with minimal CO2 emissions.Companies like Reliance Industries are also investing in green hydrogen projects aimed at decarbonizing their refining and chemical operations. By transitioning to hydrogen-based processes, the Indian chemical industry can significantly reduce its dependence on fossil fuels and lower its carbon footprint.
The Role of Green Hydrogen in India’s Transition
One of the key enablers of hydrogen technology’s success in heavy industries is the production of green hydrogen. Green hydrogen, produced through the electrolysis of water using renewable energy sources such as solar and wind, is critical for achieving carbon neutrality. India, with its abundant renewable energy potential, is well-positioned to become a global leader in green hydrogen production.
The government of India has recognized the strategic importance of hydrogen in its energy transition and has introduced the National Hydrogen Mission. The mission aims to scale up hydrogen production and utilization across sectors, with a particular focus on heavy industries. By 2030, India aims to become a major exporter of green hydrogen, supplying clean energy to both domestic industries and international markets.
Challenges and the Way Forward
While the potential of hydrogen to revolutionize heavy industry is immense, there are several challenges that need to be addressed:
- High Costs:
Currently, green hydrogen production is more expensive than hydrogen derived from natural gas or coal. The cost of renewable energy, electrolyzers, and infrastructure for hydrogen storage and transportation needs to come down for hydrogen technology to be commercially viable in heavy industries. - Infrastructure Development:
The widespread adoption of hydrogen requires significant investments in infrastructure, including hydrogen production facilities, storage tanks, pipelines, and transportation systems. Without this infrastructure in place, industries may face difficulties in accessing sufficient quantities of hydrogen to support large-scale operations. - Regulatory Support:
The Indian government will need to provide robust policy frameworks, financial incentives, and regulatory support to encourage private-sector investment in hydrogen technologies. This includes subsidies for green hydrogen production, tax breaks for hydrogen-related infrastructure, and funding for research and development initiatives.
Despite these challenges, the future looks bright for hydrogen-powered technologies in India’s heavy industry sector. Companies that invest in hydrogen now will not only benefit from reduced emissions but also gain a competitive advantage in the global market as the demand for low-carbon products increases.
Conclusion
Hydrogen technology has the potential to revolutionize heavy industries such as steel, cement, and chemical production in India. By replacing fossil fuels with clean hydrogen, these industries can significantly reduce their carbon emissions and contribute to India’s climate goals. While challenges remain in terms of cost and infrastructure, ongoing government support and private-sector innovation are likely to accelerate the adoption of hydrogen technologies. As a leader in hydrogen plant manufacturing, Hydrogen Gentech Private Limited is poised to play a key role in driving this transformation, ensuring a cleaner and more sustainable future for India’s industrial sector.